The Future of Automotive Manufacturing: Plastic Automobile Parts Mold
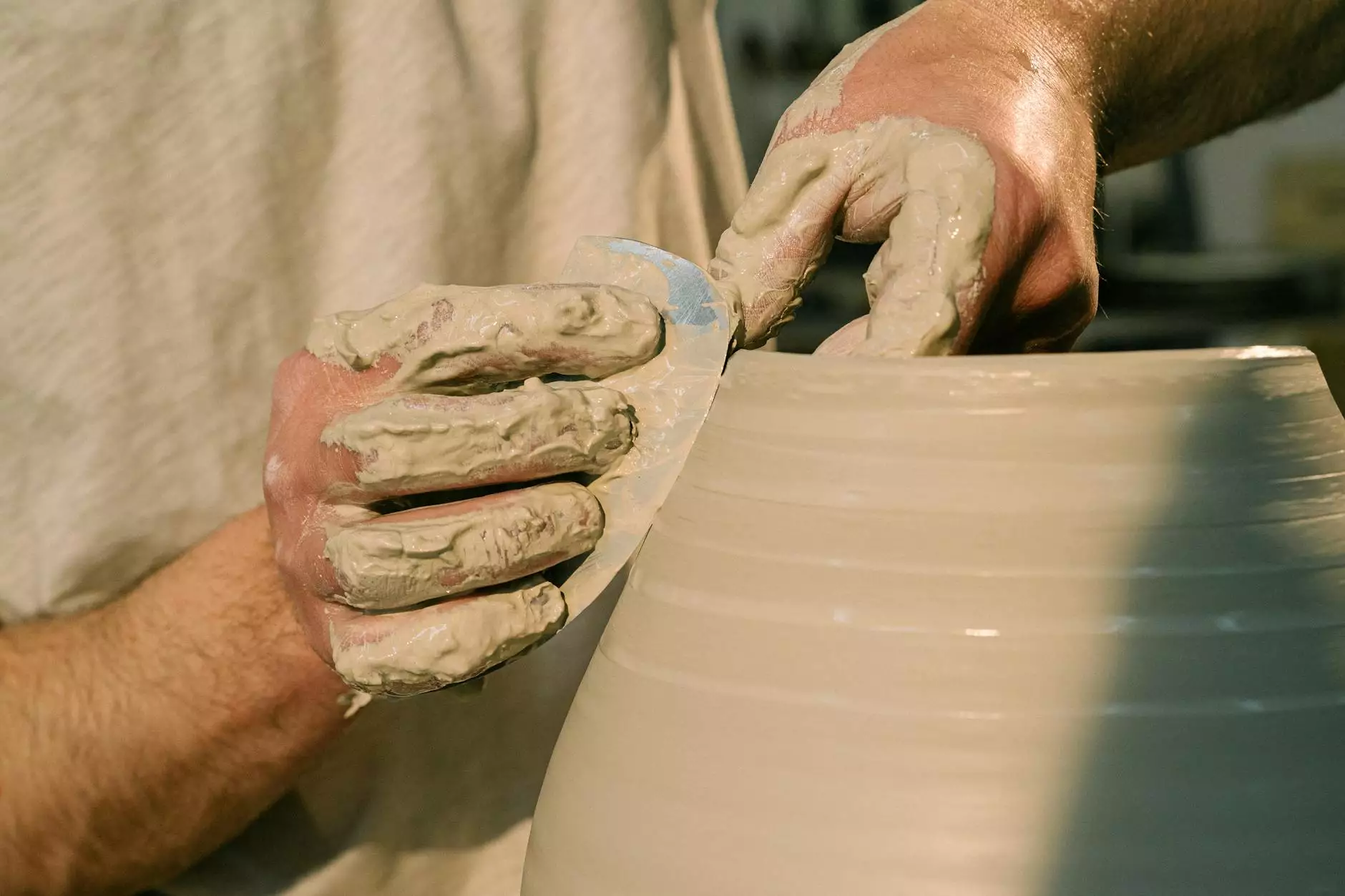
The automotive industry is undergoing a significant transformation, driven by the need for efficiency, sustainability, and cost-effectiveness. One of the key innovations fueling this change is the use of plastic automobile parts mold. This article delves into the intricacies of plastic molding technology, its advantages, and how manufacturers like Hanking Mould have positioned themselves at the forefront of this growing sector.
Understanding Plastic Automobile Parts Mold
Plastic automobile parts molds are specialized molds used in the production of various plastic components in vehicles. These molds are crucial in shaping and forming the parts that make up modern automobiles, from interior details to under-the-hood functionalities. With the rise of fuel-efficient and electric vehicles, the demand for lightweight materials has surged, making plastic a preferred choice for many car manufacturers.
The Advantages of Using Plastic in Automobile Manufacturing
The shift towards plastic is driven by several advantages it offers over traditional materials, such as metal or glass. Here are some key benefits:
- Weight Reduction: Plastic parts significantly lower automotive weight, enhancing fuel efficiency and improving performance.
- Corrosion Resistance: Unlike metals, plastics do not rust or corrode, which extends the lifespan of automotive components.
- Cost Efficiency: Plastic molds are generally more cost-effective to produce than metal molds, reducing overall production costs.
- Design Flexibility: The versatility of plastic allows manufacturers to create intricate designs and complex shapes that may be challenging with traditional materials.
- Environmental Impact: Many plastics are recyclable, contributing to more sustainable automotive production practices.
The Role of Hanking Mould in Manufacturing Plastic Automobile Parts Mold
Hanking Mould, a leading plastic mold maker and plastic injection mould manufacturer, has been at the forefront of this innovation. With years of experience, Hanking Mould has developed advanced technologies and expertise in producing high-quality plastic molds that cater to the diverse requirements of the automotive industry.
Expertise in Plastic Molding Technology
The company utilizes state-of-the-art equipment and employs skilled professionals who understand the intricacies of plastic molding. They focus on achieving precision and durability in every mold, ensuring that the finished products meet rigorous industry standards.
Customized Solutions for Manufacturers
Recognizing that each customer has unique needs, Hanking Mould offers customized solutions. They work closely with automotive manufacturers to design and produce molds tailored to specific components, allowing for optimized production processes and improved product quality.
Applications of Plastic Automobile Parts Mold in the Industry
The applications of plastic automobile parts molds are vast and varied, touching every aspect of vehicle design and functionality. Key applications include:
- Interior Components: Dashboard panels, console components, and door trim made from plastic enhance the aesthetic appeal and reduce weight.
- Exterior Parts: Bumpers, grilles, and fenders can be molded from plastic to give vehicles a sleek look while maintaining structural integrity.
- Under-the-Hood Components: Many internal engine parts are being replaced with lightweight plastic alternatives that perform efficiently under heat.
- Safety Features: Modern vehicles incorporate plastic in safety components like airbags and seat frames, contributing to overall passenger safety.
The Process of Creating a Plastic Automobile Parts Mold
The creation of plastic automobile parts molds follows several meticulous steps:
1. Design and Prototyping
It begins with the design phase, where engineers and designers collaborate to create detailed specifications for the mold. They may use computer-aided design (CAD) software to visualize the final product and make necessary adjustments before production begins.
2. Mold Fabrication
Once the design is finalized, the actual mold is fabricated. This process involves precision machining of materials like steel or aluminum, shaped to create the desired automotive component. The fabrication must be precise to ensure that the end products fit exactly as intended.
3. Testing and Quality Assurance
After fabrication, the mold undergoes rigorous testing to ensure it produces parts that meet quality standards. Adjustments may be made to improve performance and durability based on test results.
4. Production
Once testing is complete, the mold enters full-scale production. Plastic is injected into the mold under high pressure, allowing it to take the shape of the cavity inside.
5. Post-Production Finishing
Finally, the molded parts undergo finishing processes, including trimming, painting, and assembly, before being delivered to automotive manufacturers.
The Future of Plastic Molding in Automotive Manufacturing
As the automotive industry moves towards more sustainable and efficient production methods, the role of plastic automobile parts mold will only grow. Future trends indicate a shift towards:
- Advanced Materials: The development of new high-performance plastics that can withstand extreme conditions while remaining lightweight.
- Automation: Incorporating robotics and automation in the molding process to increase efficiency and reduce human error.
- Sustainable Practices: A greater emphasis on recycling and using biodegradable plastics will shape the industry’s future.
- Integration with Smart Technologies: Developing molds for components that integrate with electronic and smart technologies within vehicles.
Conclusion
The evolution of plastic automobile parts mold is a testament to the automotive industry's commitment to innovation and sustainability. Companies like Hanking Mould are leading the way in providing plastic mold maker services that not only meet current demands but also anticipate future needs within this rapidly changing sector. As consumers increasingly favor lightweight and efficient vehicles, the role of plastic parts will undoubtedly expand, driving further advancements in mold technology.
With a focus on quality, customization, and progressive technology, Hanking Mould stands ready to meet the challenges of tomorrow's automotive landscape, ensuring that they remain a vital player in this transformative industry.