Molding Plastics: A Cornerstone of Modern Business
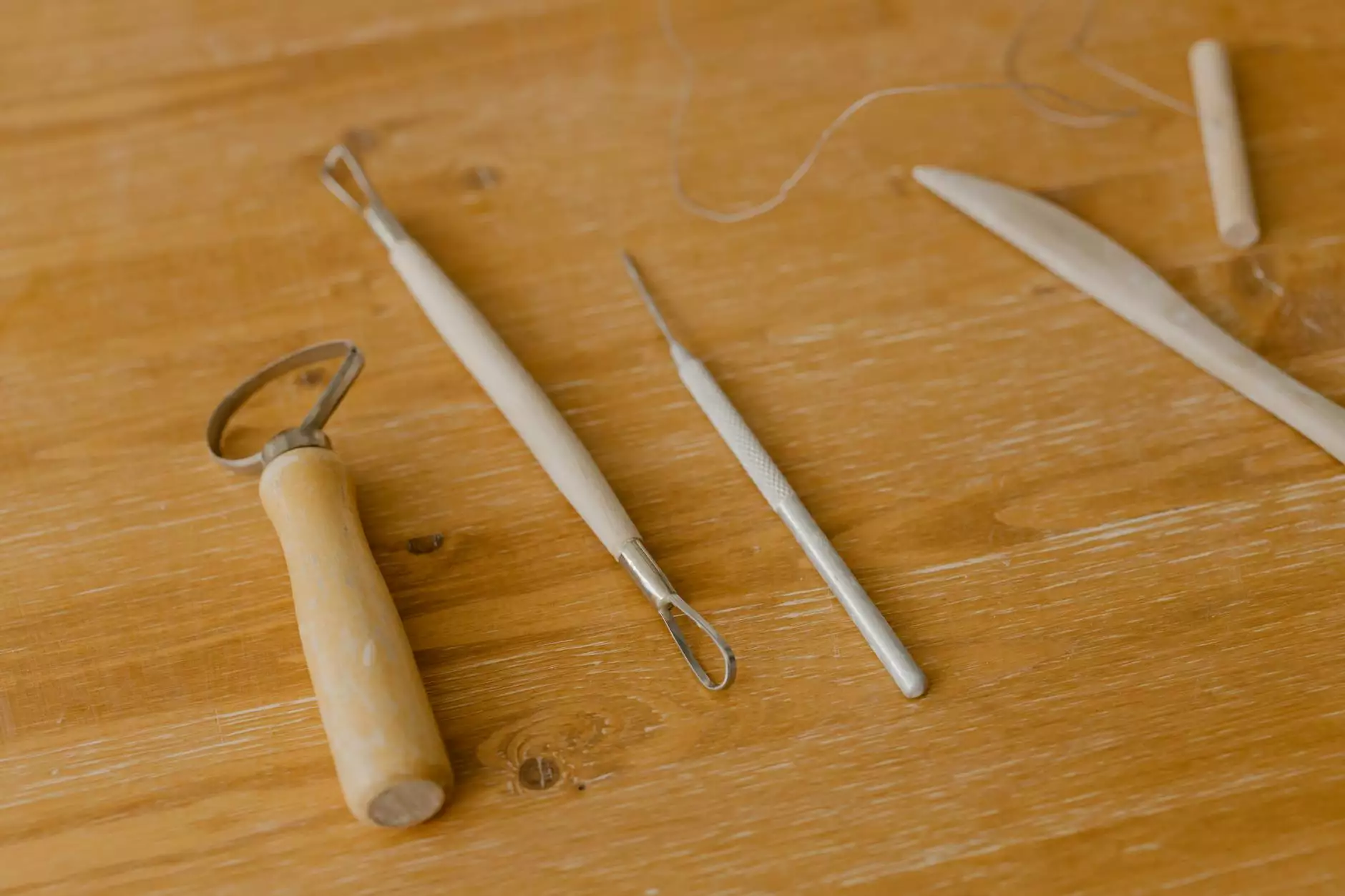
Molding plastics have become an integral part of the manufacturing landscape around the world. The versatility, durability, and cost-effectiveness of molded plastics offer substantial advantages, establishing them as essential for businesses in various sectors. As we dive into the depths of this transformative material, we'll explore its applications, techniques, benefits, and the future trends that are shaping industries.
Understanding Molding Plastics
Molding plastics refers to the process of shaping plastic material into specified forms and designs. This process is crucial in producing everything from simple household items to complex components in aerospace and medical devices. The primary methods of molding plastics include:
- Injection Molding: A process that involves injecting molten plastic into a mold where it cools and solidifies.
- Blow Molding: Mainly used for manufacturing hollow plastic products, such as bottles and containers.
- Extrusion Molding: A method of shaping plastic materials by forcing them through a die to create long, continuous shapes.
- Rotational Molding: Ideal for large, hollow products, this technique involves rotating the mold while heating it.
The Impact of Molding Plastics on Diverse Industries
The flexibility of molding plastics makes it possible to cater to diverse industries effectively. Here, we will delve into a few sectors that significantly benefit from plastic molding:
Automotive Industry
The automotive industry is a major player in adopting molding plastics due to the demand for lightweight and corrosion-resistant materials. The use of molded plastics leads to:
- Reduced Weight: Enhancing fuel efficiency.
- Cost Reduction: Lower manufacturing and material costs.
- Design Flexibility: Enabling complex shapes that improve aerodynamics.
Consumer Goods
Molding plastics plays a vital role in producing durable and attractive consumer goods. From packaging to electronics, the benefits include:
- Customization: Tailoring products to meet customer specifications.
- Durability: Offering extended product life spans.
- Branding: Enhanced design possibilities for better consumer appeal.
Healthcare Sector
The healthcare industry relies on molded plastics for creating essential medical devices and components, such as:
- Disposable syringes and medical supplies that require strict hygiene.
- Implantable devices made with biocompatible materials.
- Equipment housings that ensure safety and reliability.
The Advantages of Molding Plastics
The multitude of advantages associated with molding plastics contributes to its favorability across industries. Some key benefits include:
Cost-effectiveness
Molding plastics is often more cost-effective than other materials, especially when mass-producing items. The initial setup for molds may be high, but the per-unit cost decreases significantly with larger production runs.
Design Freedom
Plastic molding techniques allow for intricate designs that are hard to achieve with metals or other materials. This design freedom enables manufacturers to meet specific consumer needs and preferences.
Durability and Lightweight
Products made from molded plastics are typically resistant to corrosion and wear, offering longevity while being lighter than alternatives. This is particularly beneficial in applications where weight is a critical factor, such as in the automotive and aerospace industries.
Challenges in Molding Plastics
While the benefits are abundant, there are also challenges associated with molding plastics that businesses must navigate:
Environmental Concerns
Plastics have garnered criticism due to their environmental impact. However, many companies are now focusing on recyclable and biodegradable materials to mitigate these concerns.
Quality Control
Quality assurance is essential to ensure that molded products meet the necessary standards for safety and functionality. Implementing rigorous testing procedures can help manage this challenge.
Technological Adaptations
The fast-paced technological advancements can require businesses to continually adapt, often necessitating investments in new machinery or processes.
The Future of Molding Plastics
The future of molding plastics looks promising, with numerous innovations on the horizon. Key trends include:
Advancements in Bioplastics
With rising environmental concerns, the development of bioplastics – derived from renewable resources – is gaining traction. Innovations in this field could revolutionize how industries use plastics.
Smart Materials
Smart plastics that can respond to environmental stimuli are under research and development. These materials may play a role in advanced applications, enhancing functionality and usability.
Enhanced Recycling Processes
Improving recycling technologies is also key to the future of molding plastics. Companies are increasingly exploring ways to recycle plastic scrap generated during manufacturing processes, promoting sustainability.
Conclusion
In the ever-evolving landscape of modern manufacturing, molding plastics stand out as a powerhouse material that continues to reshape industries. Its ability to reduce costs, enhance designs, and contribute to sustainability efforts renders it invaluable. As technology evolves and businesses adapt, the potential of molding plastics will surely expand, offering exciting prospects for innovation and efficiency across various sectors.
For businesses looking to embrace this versatile material, partnering with a leading provider like Deep Mould can facilitate access to cutting-edge molding technologies and solutions tailored to meet specific needs. Investing in molding plastics not only enhances product quality but also ensures alignment with future industry trends.
© 2023 Deep Mould - All Rights Reserved